Understanding Cummins Parts Cost: A Detailed Overview
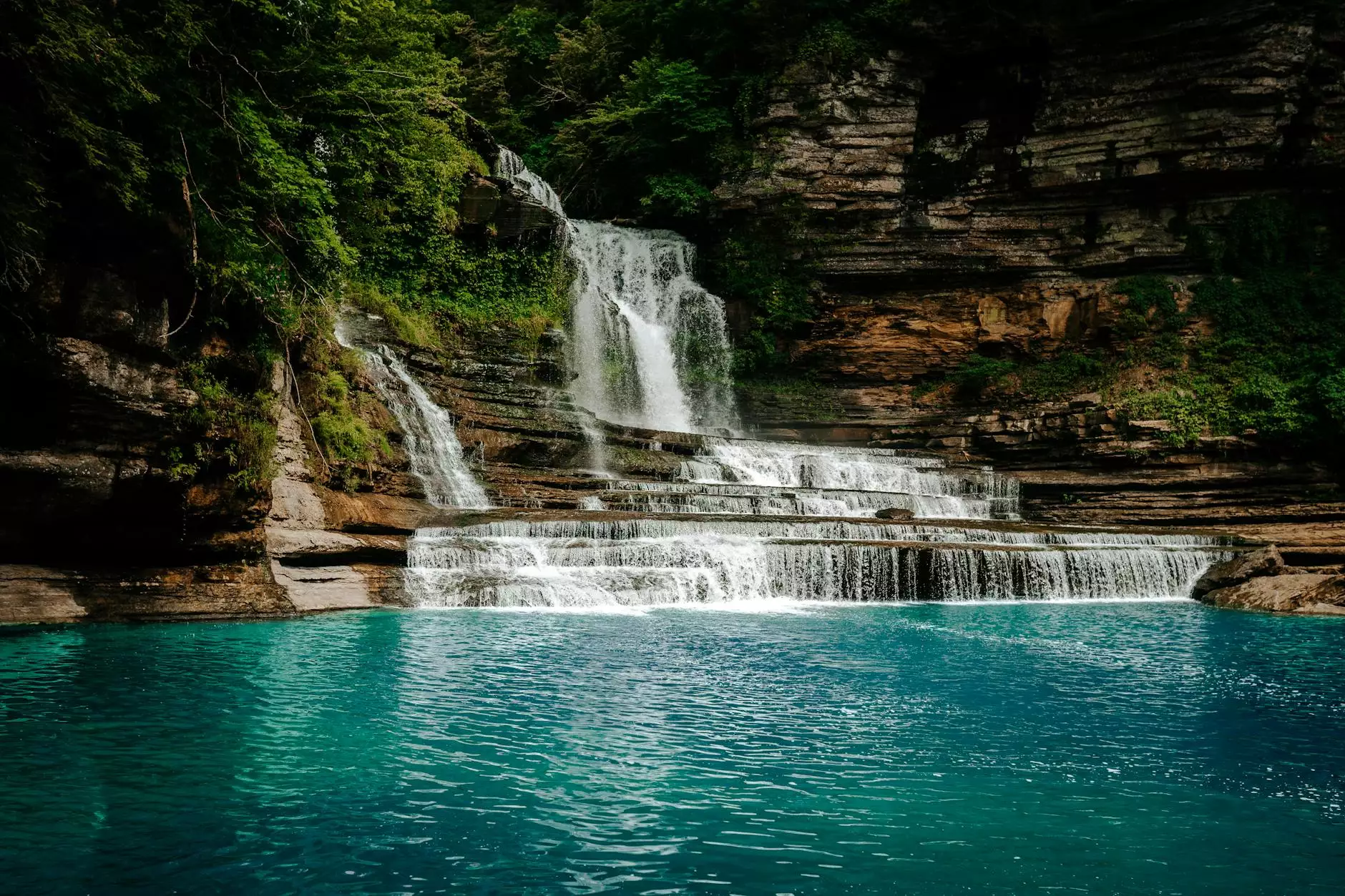
When it comes to maintaining and operating diesel engines, understanding Cummins parts cost is crucial for all business owners who rely on reliable performance. Cummins is a name synonymous with quality and durability in the diesel engine market. As a leading diesel engine manufacturer, Cummins offers a wide range of parts designed for optimal efficiency and longevity. In this article, we’ll dive deep into the factors influencing the cost of Cummins parts, types of parts available, and how to effectively manage your expenses.
Factors Influencing Cummins Parts Cost
The price of Cummins parts can vary significantly based on several factors, including but not limited to:
- Type of Part: Different components come at different price points. Engine blocks, fuel injectors, and turbochargers, for instance, will vary in cost.
- Original Equipment Manufacturer (OEM) vs Aftermarket: OEM parts are typically more expensive due to their assured quality and direct compatibility, while aftermarket parts are often less expensive but can vary in quality.
- Location: Where you purchase your parts can influence pricing significantly. Factors like shipping costs and local market conditions can play a role.
- Supplier: Different suppliers may offer varying price points based on their overhead costs, relationships with manufacturers, and purchase volume.
- Warranty and Support: Parts that come with warranties or customer support may cost more upfront but can save money in the long run through reduced failure rates.
- Volume Discounts: Purchasing parts in bulk often leads to significant discounts, which can be beneficial for businesses needing multiple components.
Types of Cummins Parts and Their Costs
To understand Cummins parts cost, it's essential to know the common categories of parts that may be required:
1. Engine Components
Engine components form the heart of any diesel engine. These include:
- Engine Blocks: Pricing can range from $2,500 to $8,000 depending on the engine model.
- Cylinder Heads: A cylinder head may cost between $1,200 and $3,500.
- Fuel Injectors: Expect to pay around $300 to $800 each.
- Pistons and Rings: The combination can cost anywhere from $200 to $1,500.
2. Turbochargers
Turbochargers enhance engine efficiency and performance:
- New turbochargers typically range from $1,000 to $3,000 depending on specifications and capabilities.
- Rebuilt turbochargers may be available for around $600 to $1,500, offering savings for those looking to reduce costs.
3. Exhaust and Emission Components
With increasing regulatory demands, components like catalytic converters and DPFs are crucial:
- Diesel Particulate Filters (DPFs): Prices often range from $1,200 to $3,000.
- Catalytic Converters: Costs can vary widely, typically between $500 and $2,500.
4. Electrical Components
These are essential for the functionality and control systems of diesel engines:
- ECUs: Engine control units (ECUs) may cost anywhere from $500 to $2,000.
- Sensors: Different sensors (temperature, pressure) range from $50 to $300 each.
How to Manage Cummins Parts Cost Effectively
Managing Cummins parts cost is essential for your business's operational efficiency. Here are some strategies to consider:
1. Build Relationships with Suppliers
Establishing strong relationships with reliable suppliers can lead to negotiated terms, discounts, and potentially better quality service.
2. Regular Maintenance
Implementing a proactive maintenance schedule can prevent catastrophic failures that require costly part replacements. By following your engine’s maintenance guidelines, you can extend the lifespan of its components, thereby reducing overall costs.
3. Consider OEM vs Aftermarket Parts
While OEM parts provide guaranteed compatibility and quality, aftermarket options can be cost-effective if sourced from reputable manufacturers. Always weigh the potential long-term benefits against initial costs.
4. Invest in Training
Training your technicians can increase efficiency in diagnostics and repairs, ultimately saving on labor costs associated with part replacements.
5. Monitor Market Trends
Keeping an eye on market prices for Cummins parts cost can help businesses purchase parts strategically, capitalizing on seasonal sales or supply shortages.
Conclusion
Understanding the intricacies of Cummins parts cost is absolutely essential for businesses that depend on reliable diesel engine performance. By carefully considering the factors influencing parts pricing, thoroughly researching the types of components needed, and employing effective management strategies, you can ensure that your operations remain both efficient and cost-effective.
In a competitive market, it is crucial to make informed decisions regarding parts sourcing and maintenance practices. By investing time and resources into understanding your engine's needs, your business can sustain its operations, save money, and ultimately thrive in the challenging landscape of diesel engine manufacturing and supply. Whether you are a seasoned expert or new to the field, the knowledge surrounding Cummins parts will serve as a valuable asset in your pursuit of excellence.