The Essential Guide to Plastic Injection Molding Factories
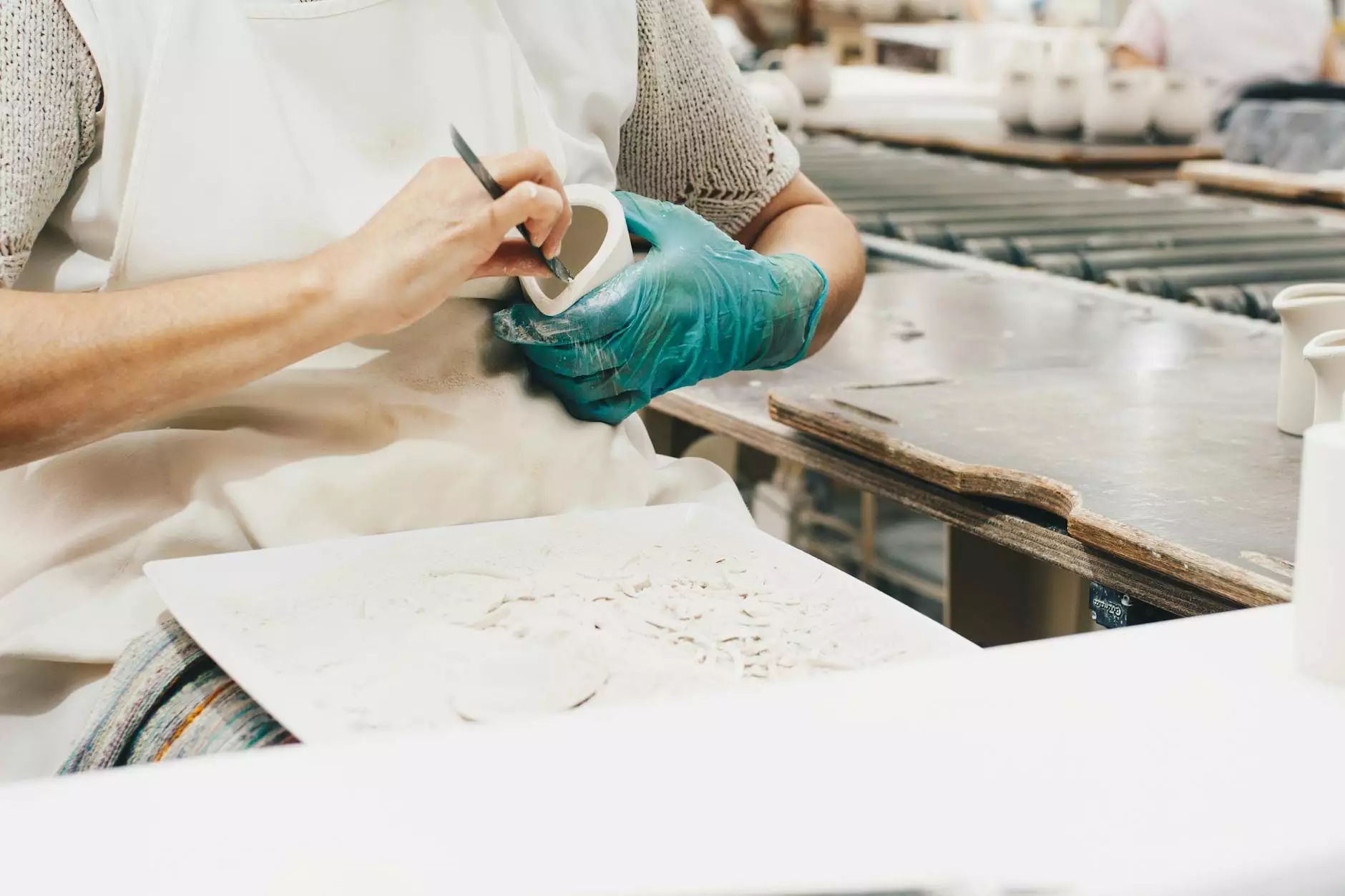
In the modern manufacturing landscape, plastic injection molding factories play a pivotal role in creating a diverse array of products. This innovative process is not only efficient but also cost-effective, providing businesses with a reliable method for producing high-quality plastic components. In this article, we will delve into the specifics of plastic injection molding, exploring its processes, advantages, applications, and future trends.
What is Plastic Injection Molding?
Plastic injection molding is a manufacturing process that involves injecting molten plastic material into a pre-designed mold. Once the plastic cools and solidifies, the mold is opened, and the finished part is ejected. This process allows for the production of intricate shapes and designs with a high degree of accuracy and repeatability.
The Process of Plastic Injection Molding
The process of plastic injection molding can be broken down into several key steps:
- Material Selection: Choosing the right type of plastic resin is critical. Thermoplastics like polyethylene, polystyrene, and polypropylene are commonly used due to their versatility and durability.
- Injection: The plastic resin is heated until it becomes molten and is then injected into the mold cavity under high pressure.
- Cooling: The molten plastic is allowed to cool and solidify within the mold. This step requires precise temperature control for optimal results.
- Ejection: Once cooled, the mold opens, and the newly formed plastic part is ejected from the mold cavity.
- Finishing: Additional processes, such as trimming, painting, or assembling, may be applied to complete the product.
Advantages of Using Plastic Injection Molding Factories
Businesses can reap numerous benefits from utilizing plastic injection molding factories. Here are some of the most significant advantages:
1. High Efficiency and Speed
The injection molding process is highly efficient, capable of producing large quantities of parts in a short amount of time. Once the mold is created, the cycle time for producing each part can be as little as a few seconds.
2. Design Versatility
Injection molding allows for an extensive range of designs and complexities that would be challenging to achieve with other manufacturing methods. This versatility enables companies to produce custom parts tailored to their specific needs.
3. Cost-Effectiveness for Large Production Runs
While the initial cost of creating molds can be high, the cost per part decreases significantly as production volume increases. This makes injection molding a highly economical option for large-scale manufacturing.
4. Material Properties
Plastic injection molding factories can utilize a variety of materials, each with unique properties. This allows manufacturers to choose materials that best suit the functionality and requirements of their products.
5. Minimal Waste
The process generates very little waste compared to traditional machining methods, as excess material can often be recycled back into the process. This contributes to a more sustainable production cycle.
Applications of Plastic Injection Molding
The applications of plastic injection molding are extensive and diverse, impacting numerous industries:
- Automotive Industry: Components such as dashboards, interior trim, and key housings are commonly produced through injection molding.
- Consumer Products: Everyday items like containers, toys, and electronics often rely on injection molded parts for production.
- Healthcare: Medical devices and components, such as syringes and protective casings, are manufactured using this process to ensure precision and compliance with health regulations.
- Electronics: The casing and internal components of various electronic devices, including smartphones and computers, are frequently created through injection molding.
- Packaging: Injection molded parts are widely used in packaging, including bottles, closures, and containers that require durability and sealability.
Choosing the Right Plastic Injection Molding Factory
Selecting the appropriate plastic injection molding factory can significantly affect your product quality, production speed, and overall costs. Here are factors to consider when making your choice:
1. Experience and Expertise
Look for factories with a proven track record in the industry. Experienced manufacturers can provide valuable insights and drive innovation in your project.
2. Technology and Equipment
Modern injection molding requires advanced machinery and technology. Ensure the factory utilizes state-of-the-art equipment to maintain precision and quality.
3. Quality Assurance
A commitment to quality assurance practices is crucial. Factories should have robust quality control measures in place to meet industry standards and your specific requirements.
4. Production Capabilities
Consider the factory's production capacity. They should be able to handle your volume requirements efficiently without compromising on quality or speed.
5. Customer Support
Effective communication and customer support are vital throughout the manufacturing process. Choose a factory that values customer relationships and is responsive to your needs.
The Future of Plastic Injection Molding
The future of the plastic injection molding industry is promising, with several emerging trends shaping its development. Here are key trends to watch:
1. Sustainable Practices
As environmental concerns rise, there is a strong push towards sustainable manufacturing practices. Many plastic injection molding factories are now investing in eco-friendly materials and processes that minimize their carbon footprint.
2. Advanced Technologies
Technological advancements such as robotics, artificial intelligence, and the Internet of Things (IoT) are enhancing efficiency and precision in injection molding processes. Factories will increasingly leverage these innovations for better productivity.
3. Customization and Rapid Prototyping
The demand for customized products continues to grow. With advancements in technology, factories are now able to offer rapid prototyping services, allowing businesses to test and refine their designs quickly.
4. Globalization and Supply Chain Optimization
As the global market expands, factories will seek to optimize their supply chains. This includes establishing partnerships worldwide to ensure a steady flow of materials and components.
Conclusion
In summary, plastic injection molding factories are integral to modern manufacturing. They offer a wealth of advantages, including efficiency, design versatility, and cost-effectiveness for large production runs. With a wide range of applications across various industries, these factories continue to evolve with emerging technologies and sustainable practices. By choosing the right factory and adapting to the latest trends, businesses can successfully harness the potential of plastic injection molding to thrive in a competitive market.