Exploring the World of Plastic Molding Electrical Applications
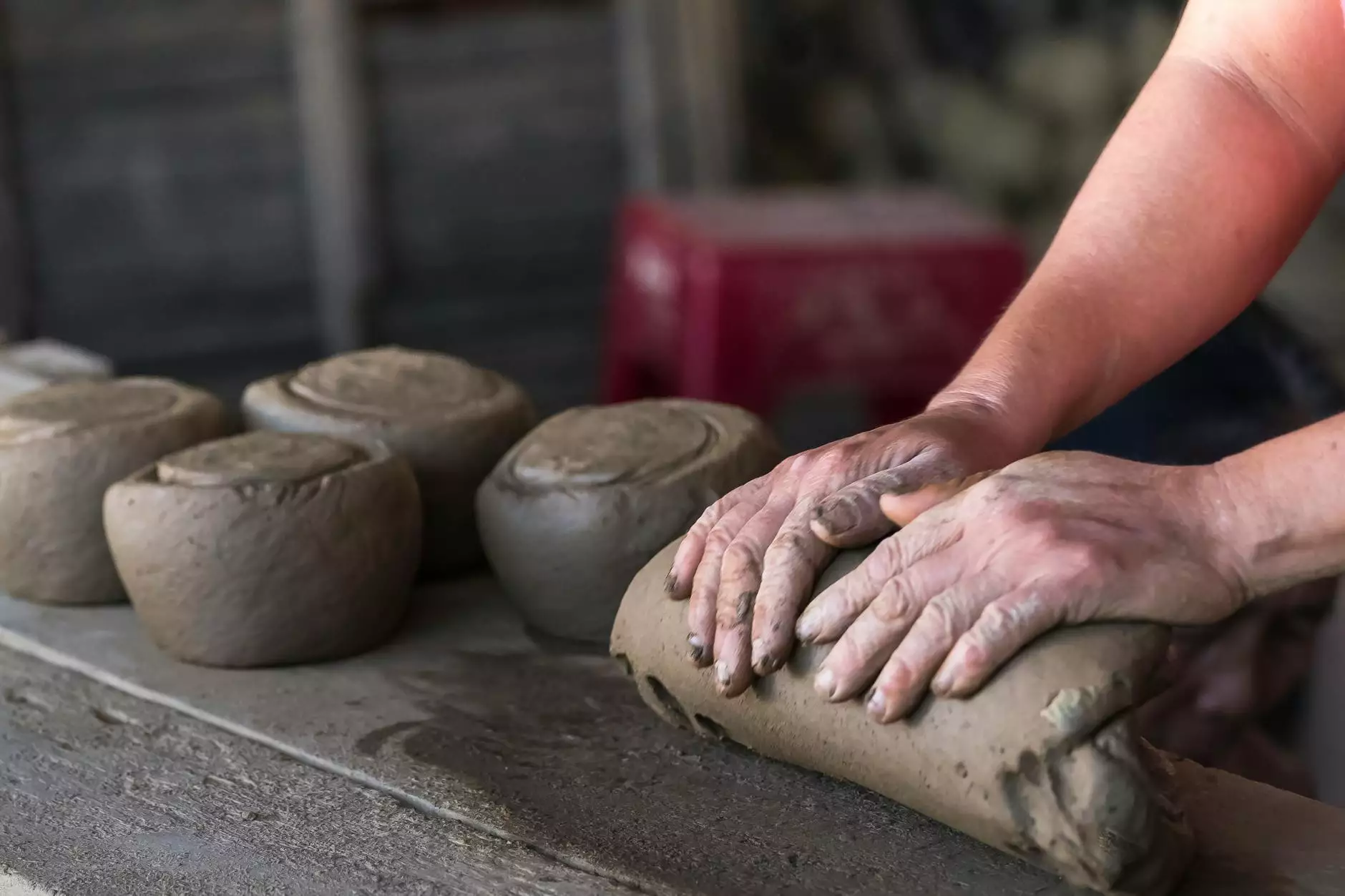
The realm of plastic molding electrical is a fascinating domain that merges technology with innovation. Plastic molding plays a pivotal role in the manufacturing of various electrical components, ensuring durability, efficiency, and safety. This article aims to provide an in-depth exploration of plastic molding in electrical engineering, highlighting its techniques, applications, and benefits.
Understanding Plastic Molding
Plastic molding is a manufacturing process that involves shaping plastic materials into specific forms. This process is critical in producing a variety of items, from household goods to industrial parts. The basic concept involves melting plastic pellets, injecting them into a mold, and allowing them to cool into a defined shape. This technique is particularly significant in the electrical sector for several reasons:
- Versatility: Plastic molding can be used to create intricate shapes and designs, making it suitable for complex electrical components.
- Cost-effectiveness: The production of items through plastic molding is often less expensive compared to other materials such as metals.
- Durability: Plastics can show remarkable resistance to moisture, chemicals, and heat, essential properties for electrical products.
The Process of Plastic Molding
Types of Plastic Molding Techniques
In the context of plastic molding electrical applications, several molding techniques are widely used:
- Injection Molding: This is the most common method where molten plastic is injected into a mold. It allows for high-volume production and can create complex shapes.
- Blow Molding: Typically used for hollow objects, this method involves inflating a heated plastic tube within a mold. It's commonly used for containers and certain electrical enclosures.
- Compression Molding: This technique is applied to thermosetting plastics. A pre-measured amount of plastic is placed into a heated mold, where it is compressed and heated until it cures.
- Rotational Molding: Often utilized for large items, this process involves rotating a mold filled with plastic, allowing the material to coat the inside uniformly.
The Injection Molding Process: A Closer Look
Injection molding is particularly crucial in electrical applications. Here’s a step-by-step breakdown of the injection molding process:
- Material Selection: The first step involves choosing the appropriate plastic material based on its properties, such as conductivity, thermal resistance, and flexibility.
- Melting: Plastic pellets are fed into a heated barrel where they are melted into a viscous state.
- Injection: The molten plastic is injected into a carefully designed mold where it takes the shape of the desired part.
- Cooling: After injection, the material is allowed to cool and solidify within the mold.
- Demolding: The final step is removing the solidified part from the mold, ready for further processing or assembly.
Applications of Plastic Molding in Electrical Engineering
Plastic molding has a multitude of applications within the electrical industry. Here are some key areas where it is particularly beneficial:
1. Electrical Connectors
Connectors are vital components in almost every electronic device. The use of molded plastic in these connectors provides various advantages:
- Electrical Insulation: Plastics are excellent insulators, minimizing the risk of short-circuits.
- Custom Tolerance: Molding allows for precise dimensions, ensuring a perfect fit between male and female connectors.
- Color Coding: Different colored plastics can enhance the organization of complex wiring systems.
2. Circuit Board Enclosures
Enclosures protect sensitive electronic components from environmental hazards. Through plastic molding, manufacturers can create:
- Lightweight Designs: Plastic enclosures are much lighter than their metal counterparts, which is crucial for portable devices.
- Heat Resistance: Certain plastics can withstand high temperatures, safeguarding the electronic components inside.
3. Household Electronics
Many household devices—from kitchen appliances to personal gadgets—rely on plastic molding in their design. Benefits include:
- Ergonomic Shapes: Molding enables the creation of user-friendly designs that fit comfortably in the hand.
- Robustness: Molded components can withstand daily wear and tear, enhancing the lifespan of the electronics.
Advantages of Using Plastic Molding in Electrical Applications
The integration of plastic molding in electrical applications does not just stop at being a production method. It brings along a host of benefits that can significantly influence the design and functionality of electrical components:
Cost Efficiency
One of the most significant advantages of plastic molding is its cost-effectiveness:
- High-volume production leads to reduced per-unit costs.
- Lower raw material costs mean significant savings, especially in high-demand markets.
Design Flexibility
Molding offers a remarkable capacity for innovation:
- Complex geometries can be achieved with minimal additional costs.
- Rapid prototyping enables quicker design adjustments and upgrades.
Durability and Reliability
Products made from molded plastics are not only resilient but also reliable. This is crucial for electrical applications where:
- Longevity is essential due to the high cost of replacements.
- Dependability is critical to ensure safety and functionality.
The Future of Plastic Molding in Electrical Applications
As technology continues to evolve, so do the methods and materials used in plastic molding. The electrical industry is witnessing exciting advancements:
- Smart Materials: The introduction of smart polymers that can change properties based on environmental stimuli could revolutionize electrical components.
- Sustainable Practices: With increasing emphasis on sustainability, the use of biodegradable plastics in molding processes is gaining traction.
- 3D Printing: The fusion of traditional molding techniques and 3D printing technology is expected to lead to unprecedented customization possibilities.
Conclusion
In conclusion, the importance of plastic molding electrical applications cannot be overstated. This innovative manufacturing process enables the production of durable, cost-effective, and complex electrical components essential for modern technology. As industries continue to evolve, embracing advancements in molding techniques will play a crucial role in driving efficiency and performance across various applications.
For those looking to expand their understanding of the intersection between plastic molding and electrical engineering, organizations like Deep Mould offer insights and services that can aid in the advancement of your projects.